Pentagon Secures U.S. Magnet Sovereignty
Critical minerals, policy, and the energy transition
11 July 2025
A Fully Sovereign Mine-to-Magnet REE Supply Chain
Washington’s 10 July 2025 announcement marks the most significant U.S. industrial intervention in critical minerals since the Cold War. It replaces an 80%-China-dominated neodymium-iron-boron (NdFeB) magnet supply chain with a fully sovereign American ecosystem. Designed to secure strategic autonomy and eliminate long-standing geopolitical exposure, the initiative goes far beyond restoring domestic capacity. It delivers a permanent structural shift, transforming rare-earth magnet production from a critical vulnerability into a durable strategic advantage at the heart of America’s reindustrialisation and defence posture.
To deliver this transformation, the agreement sets out a comprehensive industrial blueprint that fuses public-sector commitment with private execution. It lays the foundation for a fully integrated rare-earth magnet supply chain on U.S. soil, built for resilience, scale and speed. The following foundations define the structure and scope of the initiative:
-
Public-private scale – The agreement combines Pentagon equity, targeted federal loans, a ten-year 100% DoD offtake commitment covering defence consumption and commercial syndication, and private-sector capital, underwriting the entire mine-to-magnet value chain from ore extraction through metal conversion to finished magnet manufacturing.
-
Re-shoring control – China’s grip on more than 80% of global NdFeB magnet output has historically given it powerful leverage over aerospace, defence, automotive and clean-energy sectors. This partnership breaks that dependency by placing extraction, separation, metal production and magnet fabrication entirely on U.S. soil.
-
Domestic magnet build-out – MP Materials will first triple output at its Texas hub by adding a 2 ktpa expansion to the existing 1 ktpa Independence line, lifting that site to 3 ktpa. This near-term step is followed by the 7 ktpa 10X green-field facility, raising aggregate U.S. magnet capacity to 10 ktpa and eliminating decades of reliance on foreign supply.
-
Mountain Pass expansion – The upgraded California complex will feature new processing circuits for dysprosium, terbium and samarium, converting U.S.-mined ore into the high-performance heavy rare earths essential for defence and aerospace-grade magnets. These materials, previously refined almost exclusively in Asia, will now flow into both the 10X and Independence plants.
-
Vertically integrated production – The partnership completes the missing link in U.S. supply security by establishing an unbroken domestic chain from mined concentrate to finished magnet, ensuring resilient throughput across civilian and military programmes.
-
Fast-track timeline — Site selection for the 10X facility is currently underway. Engineering, permitting, and state incentive negotiations are expected to conclude within twelve months. Construction will begin in 2026, with the first commercial product expected in 2028. The build-out is projected to create thousands of skilled jobs and generate a multidecade tax base in the host state.
Mountain Pass leads the U.S. rare-earth rebuild
As the anchor of America’s rare-earth revival, Mountain Pass has steered the industry for nearly eight decades. Discovered in the 1940s and brought into commercial production in the 1950s, the mine quickly became a strategic U.S. asset during the Cold War, supplying most of the world’s rare-earth oxides throughout the 1960s, 1970s, and 1980s. Operated by Molybdenum Corporation of America, later Molycorp, it furnished critical inputs for colour televisions, fluorescent lighting, catalysts, and early magnet technologies, and by the 1980s it was the world’s leading producer of separated rare-earth elements.
After decades of global dominance, Mountain Pass slipped into decline as rising environmental-compliance costs, low-priced Chinese exports, and limited federal industrial policy forced the mine into care-and-maintenance during the late 1990s and early 2000s. The downturn culminated in Molycorp’s 2015 bankruptcy, yet that low point catalysed the site’s strategic revival when MP Materials acquired the asset in 2017 with private backing and U.S. Department of Energy support, then launched the US$1.7 billion Project Phoenix to restart mining, reactivate separation circuits and rebuild a vertically integrated platform. Since 2020, Mountain Pass has re-emerged as the largest rare-earth source in the Western Hemisphere and now sits at the centre of Washington’s drive for technological sovereignty, underpinning defence systems, clean-energy technologies and broader economic resilience.
Key attributes include:
-
World-class geology – The Precambrian carbonatite hosts 8–12% total rare-earth oxides (TREO), one of the highest natural grades on record. In-situ resources exceed 20 million tonnes of ore, ensuring decades of feedstock. The deposit contains the full lanthanide suite, comprising light, medium and heavy elements, absent only the short-lived radioisotope promethium.
-
Scaled output – Following a $1.7 billion upgrade under Project Phoenix, Mountain Pass delivered 45 ktpa of REO concentrate in 2024, including 1.3 ktpa of separated NdPr oxide, representing approximately 16% of global NdPr supply. Capacity is expected to rise to 60 ktpa as downstream expansions advance, anchoring long-term supply of magnet-grade feedstock.
-
Current product slate – The site currently markets three commercial oxides, NdPr, cerium, and lanthanum, and produces a SEG+ concentrate containing samarium, gadolinium, dysprosium, terbium, and other heavy rare earths, including yttrium. This material is being stockpiled to supply the heavy-rare-earth separation circuits now under construction, ensuring no strategic elements are lost.
-
Heavy-REE expansion – Backed by a $150 million DoD loan, new solvent-extraction banks and ion-exchange stages will separate dysprosium, terbium, and samarium by 2028, removing the last major U.S. dependency on imported heavy rare earths. Previously refined almost exclusively in Asia, these materials will now be upgraded onshore and flow into the 10X and Independence plants to support advanced magnet manufacturing for hypersonic, space, and naval platforms.
-
Environmental stewardship – Mountain Pass operates the industry’s largest dry-stack tailings facility and recycles more than 95% of process water through a zero-liquid-discharge circuit, essential in the arid Mojave Desert. On-site solar infrastructure and a forthcoming 100 MWh battery system are expected to further reduce diesel use and have contributed to a 20% reduction in GHG intensity since 2018.
-
Strategic synchronisation – Heavy-REE output from Mountain Pass will ramp in parallel with the 10X and Independence facilities, completing a 10 ktpa domestic magnet production pathway and establishing full-spectrum U.S. control over magnet-grade rare-earth inputs.
Financial framework backing U.S. magnet independence
To match the scale and urgency of the supply chain transformation, the Department of Defense has crafted a robust financial architecture that delivers long-term stability, protects against market volatility, and accelerates industrial scale-up. The structure blends equity, loans, price guarantees, and offtake commitments into a framework designed to support strategic autonomy while anchoring investor confidence. Key components of the financial platform include:
-
Strategic equity stake – The Pentagon will invest $400 million in convertible preferred equity priced at $30.03 per share, accompanied by warrants that bring its ownership to approximately 15% on an as-converted, as-exercised basis. The equity carries a 7% payment-in-kind dividend, aligning public-sector capital with MP’s long-term growth and profitability.
-
Targeted loan for separation expansion – A $150 million, 12-year government loan will fund new heavy rare-earth circuits at Mountain Pass, enabling domestic production of dysprosium, terbium, and samarium—materials critical to next-generation military and aerospace systems.
-
Fully secured construction finance – MP has secured commitment letters from JPMorgan Chase and Goldman Sachs for up to $1.0 billion in construction financing for the 10X magnet facility, ensuring the project is fully capitalised ahead of groundbreaking.
-
Price floor protection – A ten-year price-floor mechanism guarantees MP a minimum of $110/kg for all neodymium-praseodymium (NdPr) products sold or stockpiled. The Department will compensate the company for any shortfall between market prices and the floor, while capturing 30% of upside once prices exceed the benchmark.
-
Guaranteed demand with upside sharing – A ten-year offtake agreement requires defence and authorised commercial buyers to purchase 100% of magnet output from the 10X facility. The structure guarantees a minimum $140 million in annual EBITDA, and splits profits equally with MP Materials above $170 million, aligning public and private incentives while preserving shared benefits from scale, efficiency and market growth.
-
Long-term earnings visibility – Taken together, these protections create a stable, scalable cash-flow platform that MP management projects will deliver over $650 million in annual EBITDA at current market prices, providing rare forward visibility and strong alignment between public and private objectives.
This financial framework de-risks capital deployment by embedding national security priorities directly into the structure of the U.S. rare-earth magnet market, enabling rapid mobilisation of resources, resilience to external shocks, and predictable investment returns.
National security and economic impact
This partnership reflects the urgent national-security imperative to secure a sovereign supply of neodymium-iron-boron (NdFeB) magnets—core components of modern defence systems, and to prevent foreign adversaries from disrupting critical U.S. military procurement. By bringing magnet production fully onshore, it shields key DoD acquisition programs, such as F‑35 aircraft, hypersonic vehicles, and precision-guided munitions, from supply shocks and foreign coercion, while unlocking a cascade of industrial and economic opportunities.
-
Defence-grade supply assurance – A sovereign magnet supply chain now underwrites uninterrupted access for F-35 flight-control actuators, the newly contracted F-47 sixth-generation fighter championed by President Trump, precision-guided munitions, hypersonic glide vehicles, naval propulsion, satellite constellations and next-generation electric-drive systems, insulating U.S. forces from geopolitical shocks.
-
Thermal and radiation resilience – New dysprosium, terbium and samarium circuits at Mountain Pass will yield high-temperature, radiation-tolerant magnets that meet the extreme performance demands of aerospace, space and nuclear platforms.
-
Procurement-programme continuity – Steady domestic magnet output lets prime contractors—including Boeing for the F-47, Lockheed Martin for the F-35, Northrop Grumman for the B-21 and RTX for hypersonic missiles—keep production on schedule and within budget, shielding multi-billion-dollar DoD acquisitions from supply-chain disruption.
-
Allied contract continuity – With magnets no longer sourced from adversary-controlled supply chains, the U.S. can confidently sustain F-35 deliveries to 19 partner nations and new F-47 export prospects, honouring long-term FMS agreements such as Germany’s expanded order for 50 aircraft and Romania’s 2024 Letter of Acceptance.
-
Template for future strategic materials – The public-private model established through this partnership sets a clear and replicable precedent for securing other critical inputs. It provides a blueprint for future interventions in battery-grade lithium, semiconductor-grade gallium, high-purity graphite, and other strategically essential minerals identified in GAO supply-chain risk assessments, positioning Washington to extend its industrial sovereignty across sectors vital to both national defence and clean-energy deployment.
-
Dual-use industrial spillovers – Beyond military applications, domestically produced NdFeB magnets are essential for offshore wind turbines, industrial robotics, high-performance electric motors, and automated manufacturing, directly supporting U.S. energy transition and reshoring efforts.
-
Alignment with federal incentives – U.S.-made NdFeB magnets will support offshore wind turbines, industrial robotics and high-efficiency EV motors, dovetailing with Inflation Reduction Act and CHIPS Act incentives while creating thousands of skilled American jobs.
-
Allied-market leverage – As Europe, Japan and Australia seek non-Chinese magnet sources, MP Materials can meet allied demand, converting a once-peripheral U.S. mine into the cornerstone of a geopolitically vital global chain.
Through this framework, rare-earth magnet production is elevated to a core element of U.S. defence and industrial policy. It safeguards America’s technological edge, secures programmes such as the F-47, fulfils allied contracts, reinforces global leadership in strategic materials and drives the next wave of American reindustrialisation.
Second-wave build-out broadens U.S. rare-earth capacity
A second wave of rare-earth infrastructure is advancing across the United States, reinforcing MP Materials’ mine-to-magnet platform and addressing remaining vulnerabilities in heavy-oxide separation and magnet production. In Hondo, Texas, Lynas Rare Earths is constructing a 5 ktpa light-oxide refinery that will convert imported carbonate into NdPr oxide and a dedicated SEG stream comprising samarium, europium, and gadolinium (Sm–Eu–Gd). The project is partially funded through a U.S. Department of Defense Title III award, embedding it within the national industrial base strategy. Detailed engineering is approaching completion, key permits have been secured, and first production for defence and commercial offtakers is scheduled for 2026.
Further west, the Round Top project near Sierra Blanca is moving through final design. Texas Mineral Resources and USA Rare Earth plan to leach, ion-exchange, and separate a heavy-rare-earth-rich ore body containing sixteen lanthanides plus lithium and gallium. This material will supply USA Rare Earth’s Stillwater magnet plant, integrating mine-to-magnet production at a single corporate level.
Utah offers a parallel oxide stream. Energy Fuels is expanding the White Mesa mill to move beyond its current NdPr line and produce six separated oxides, including dysprosium and terbium, at commercial scale as early as 2026. The mill processes monazite sands imported from Georgia and remains one of the few U.S. facilities licensed to manage associated thorium by-products, enhancing feedstock flexibility. Wyoming adds pilot-scale optionality: Rare Element Resources has begun civil works on a hydrometallurgical demonstration plant at Upton, partly funded by the Department of Defense’s IBAS programme. The facility will process Bear Lodge ore for up to fifteen months starting in 2025, generating design data for a full-scale commercial plant.
Magnet capacity is rising in tandem. USA Rare Earth has completed a 310,000 ft² sintered magnet "Innovation Lab" in Stillwater, Oklahoma, designed for 3 ktpa of NdFeB output and slated for first commercial production in the first half of 2026. In San Marcos, Texas, Noveon Magnetics is scaling a 1 ktpa facility that up-cycles end-of-life magnets into new NdFeB products, claiming a 90% energy saving over conventional processing routes. The plant forms part of a broader effort to establish circular magnet supply chains within U.S. borders.
Collectively, these facilities broaden the U.S. rare-earth footprint beyond Mountain Pass. Lynas and White Mesa provide dual-source NdPr supply, Round Top and Energy Fuels address heavy-oxide requirements, and USA Rare Earth plus Noveon deliver early domestic sintering capacity ahead of MP’s 10 ktpa pathway. MP’s Independence facility, now operating at 1 ktpa, adds a further layer of resilience. For the first time since the 1980s, multiple U.S. plants are being built in parallel, enabling ore-to-magnet production entirely within national borders and materially reducing dependence on Asia-centred supply chains.
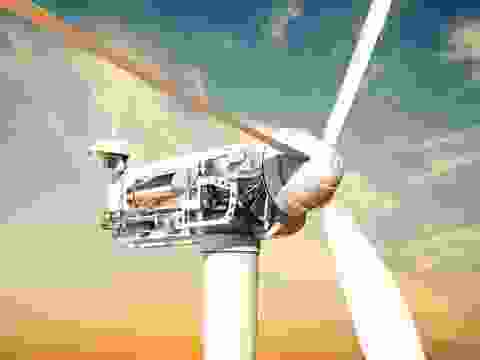
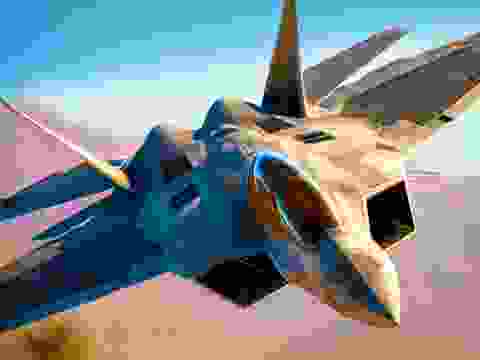
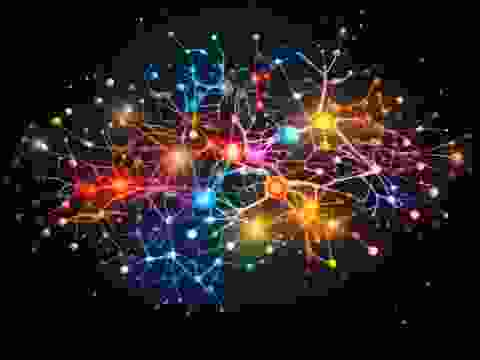
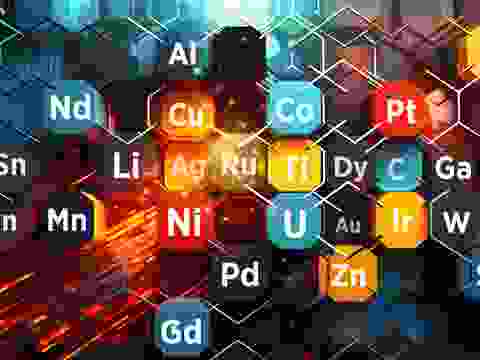
Meet the Critical Minerals team
Trusted advice from a dedicated team of experts.
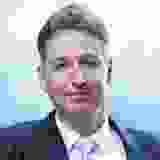
Henk de Hoop
Chief Executive Officer
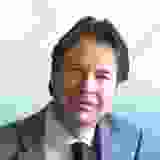
Beresford Clarke
Managing Director: Technical & Research
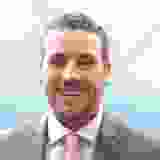
Jamie Underwood
Principal Consultant
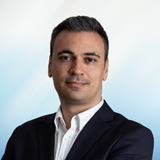
Ismet Soyocak
ESG & Critical Minerals Lead
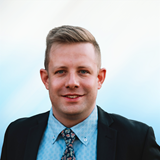
Rj Coetzee
Senior Market Analyst: Battery Materials and Technologies
Brought to you by
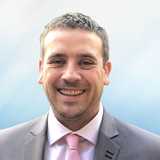
Jamie Underwood
Principal Consultant
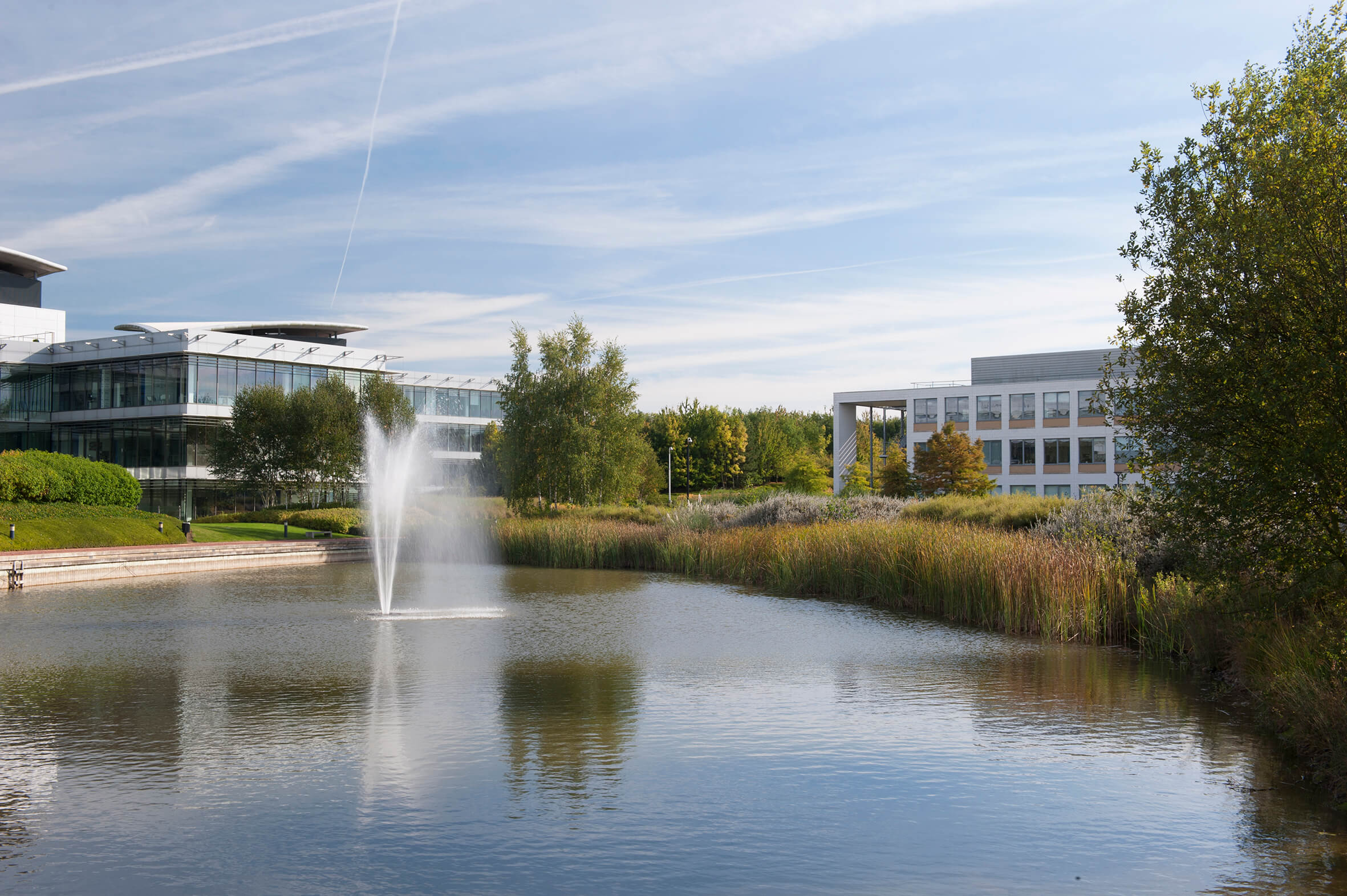
How can we help you?
SFA (Oxford) provides bespoke, independent intelligence on the strategic metal markets, specifically tailored to your needs. To find out more about what we can offer you, please contact us.