The Iridium Market
Critical Minerals and The Energy Transition
Navigating the Iridium Market
Iridium is one of the rarest and most corrosion-resistant elements on Earth, distinguished by its high melting point, electrochemical durability, and mechanical resilience in extreme environments. As a platinum group metal (PGM), it is critical to proton exchange membrane (PEM) electrolysis, satellite propulsion systems, high-temperature crucibles, and medical isotopes used in cancer treatment. Iridium’s role in PEM water electrolysers is especially strategic, given its unmatched stability in acidic, high-voltage conditions, making it vital to green hydrogen production. It also supports spaceflight, brain–computer interfaces (neuroelectronics), and precision optics, where reliability under thermal and oxidative stress is paramount. Global iridium supply is tightly constrained, being sourced almost exclusively as a by-product of platinum and nickel mining in South Africa and Russia. With no viable substitutes in its core applications and rapidly increasing demand from the hydrogen economy, aerospace, and medical technology sectors, iridium is emerging as a critical bottleneck material. SFA (Oxford)'s explores many of iridium’s end-uses, highlighting its growing relevance in the transition to a connected, secure, and sustainable global economy.
Iridium price news and insights
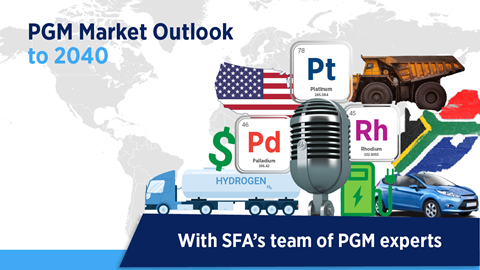
SFA's latest podcast: PGM markets out to 2040
11 November 2024
The latest SFA podcast episode examines how evolving trends in transportation and energy are reshaping the platinum group metals markets.
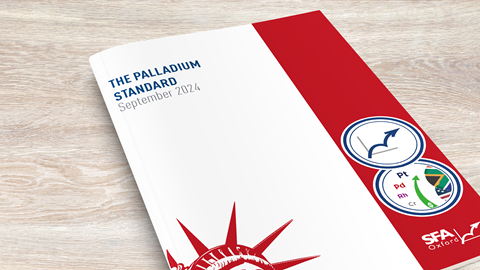
The squeeze is on: Managing the margins
10 September 2024 | Dr Ralph Grimble
PGM miners’ revenues have collapsed with the fall in palladium and rhodium prices. The little-mentioned chrome has become an important contributor.
Iridium’s outlook linked to hydrogen economy wariness
21 October 2024 | SFA (Oxford) & Heraeus
Chinese heavy-duty vehicle platinum demand could be ready for a rise
7 October 2024 | SFA (Oxford) & Heraeus
Where does the palladium market go from here?
23 September 2024 | SFA (Oxford) & Heraeus
The Chinese car market in 2024 – PHEVs, subsidies and palladium
19 August 2024 | SFA (Oxford) & Heraeus
An introduction to iridium
Iridium demand and end-uses
Iridium, one of the rarest and most corrosion-resistant elements in the platinum group metals (PGMs), plays an indispensable role in a wide range of high-performance technologies. Known for its exceptional chemical inertness, high melting point, and mechanical hardness, iridium is used where extreme durability, stability, and conductivity are required. Although global production is extremely limited, iridium’s importance is growing across clean energy, aerospace, electronics, medical, and specialised industrial sectors, and is a critical enabler of high-performance systems where no viable alternatives exist.
The most prominent and fastest-growing use of iridium is in proton exchange membrane (PEM) water electrolysers, where it serves as the preferred catalyst on the oxygen evolution reaction (OER) side. Iridium’s resistance to oxidative degradation under strongly acidic and high-voltage conditions makes it functionally irreplaceable in PEM systems. With PEM electrolysis expected to dominate green hydrogen production in high-purity and space-constrained applications, demand for iridium is forecast to rise steeply over the next decade. However, iridium’s extreme scarcity and high cost present serious constraints, leading to intensified research into load minimisation, thin-film deposition, and alloying strategies.
Iridium is also used in PEM fuel cells, though to a lesser extent than platinum. It is sometimes alloyed with platinum on the hydrogen electrode to enhance stability and extend catalyst life under demanding start-stop cycling conditions. These applications are critical for backup power systems, military-grade fuel cells, and emerging heavy-duty hydrogen mobility platforms.
In the chemical sector, iridium serves as a highly effective catalyst in several precision processes. One of the most established is the Cativa process for acetic acid production, where iridium has largely replaced rhodium due to superior performance and cost-effectiveness. Iridium complexes are also used in hydrogenation, hydrosilylation, and carbon-carbon bond formation, particularly in high-end pharmaceutical synthesis. These catalysts offer high selectivity and turnover frequencies, supporting cleaner, more efficient chemical production.
In electronics and data storage, iridium is used in the production of hard disk drives and non-volatile memory devices. It serves as a conductive barrier layer in advanced semiconductor architecture and is under investigation for next-generation resistive RAM (ReRAM) and magnetic tunnel junctions. Iridium’s stability at the nanoscale makes it valuable in highly miniaturised and high-speed circuitry. Its use is expanding in microelectronic sensors and components designed to operate under elevated thermal or oxidative stress.
In the aerospace and defence sectors, iridium is applied in thermocouples, high-temperature crucibles, and engine components where performance must be maintained in oxidising environments above 2000°C. Iridium is alloyed with platinum in ignition systems, satellite thrusters, and aerospace-grade spark plugs. It is also used in spaceflight hardware for deep-space propulsion and radiation-resistant instruments. The metal’s resilience under extreme mechanical and thermal stress has made it a material of choice in both civilian and military aerospace engineering.
In medicine, iridium is used in radioisotope form (Ir-192) for cancer brachytherapy, where it delivers targeted gamma radiation to tumours with minimal impact on surrounding tissues. It is also employed in surgical instruments and biomedical sensors, valued for its biocompatibility and chemical inertness. Iridium electrodes are used in neural stimulation devices and brain–computer interface research, where stability and signal fidelity are critical.
Iridium also finds use in glass and LED manufacturing, particularly in high-temperature crucibles used for growing synthetic single crystals and optical materials. Iridium’s ability to retain shape and resist corrosion in molten oxide environments makes it essential for producing laser-grade optical components and high-purity sapphire substrates.
In jewellery and luxury goods, iridium is used as an alloying agent in platinum jewellery to enhance hardness and scratch resistance. Though niche in volume, iridium’s use in watches, pens, and high-value design pieces continues to add to its aesthetic and mechanical appeal.
Iridium also supports a range of emerging technologies. It is being investigated for use in quantum computing, spintronic devices, and photoelectrocatalytic water splitting, where its conductivity and stability in extreme redox environments are advantageous. Iridium-based organometallic compounds are central to research on organic light-emitting diodes (OLEDs), particularly in high-efficiency phosphorescent emitters for displays and lighting.
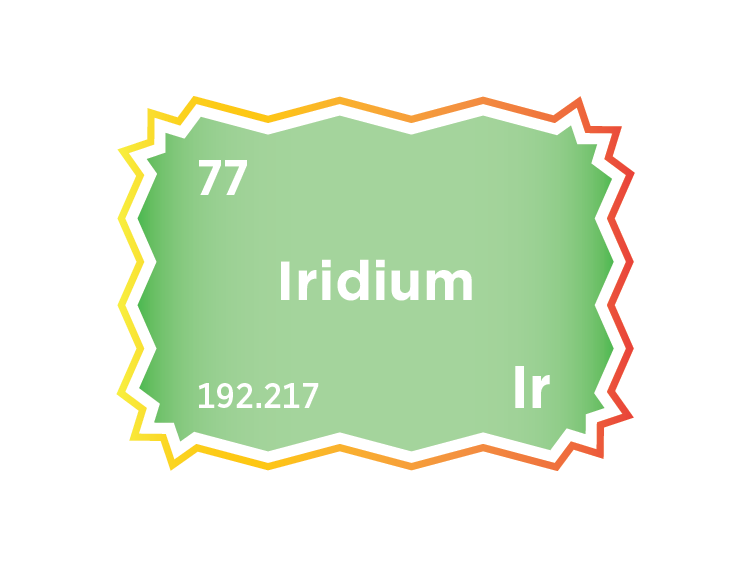
Iridium supply
Iridium supply is extremely limited and geographically concentrated, with over 95 percent of global primary production originating as a by-product of platinum and nickel mining in South Africa and Russia. South Africa’s Bushveld Complex is the dominant source, accounting for more than three-quarters of global iridium output, while Russia’s Norilsk-Talnakh region provides most of the remainder. Smaller contributions come from Canada’s Sudbury Basin, with minor trace production in Zimbabwe, Finland, and the United States. This dependence on a small number of jurisdictions, combined with iridium’s low abundance and specialised refining requirements, renders the supply chain highly vulnerable to disruption.
Primary iridium is not mined in its own right but is recovered in very small quantities during the refining of PGM concentrates. It typically occurs at concentrations below 0.1 gram per tonne in ore bodies and is separated from other PGMs via complex hydrometallurgical processes involving solvent extraction, precipitation, and electrorefining. Because iridium is tied to platinum and nickel production, its supply is inelastic and largely unresponsive to changes in standalone iridium demand. This structural limitation contributes to extreme price volatility and periodic shortages, particularly as demand rises in critical applications such as hydrogen electrolysis and aerospace propulsion.
Secondary iridium supply remains limited, but it is growing steadily due to increasing recovery from spent catalysts, crucibles, thermocouples, and biomedical devices. Recycling takes place through both open-loop and closed-loop systems, with the glass, chemical, and medical sectors providing the most consistent streams. However, recovery is technically challenging due to low iridium concentrations, contamination risks, and the harsh conditions under which iridium is used. Despite these constraints, high-purity secondary iridium is essential for applications such as PEM electrolysers and space-grade alloys, where performance requirements are stringent.
South Africa’s role as the cornerstone of global iridium production introduces a number of strategic and operational risks. The country’s PGM industry is impacted by electricity shortages, ageing infrastructure, labour unrest, and increasing ESG expectations. Russia’s contribution, primarily through Norilsk Nickel, is under growing scrutiny as a result of international sanctions, export controls, and investment restrictions. Other producers, such as Zimbabwe and Canada, offer only limited scope for expansion. These risks have prompted renewed calls for diversified refining hubs, enhanced stockpile management, and strengthened secondary recovery pathways.
Environmental considerations are also shaping the future of iridium supply. The energy intensity of deep-level mining and the chemical complexity of iridium separation make refining emissions- and resource-intensive. As green hydrogen, medical technology, and aerospace sectors demand responsibly sourced inputs, ESG-aligned certification and lifecycle transparency are becoming increasingly important. Downstream users, particularly in the hydrogen economy, are seeking assurance that iridium is sourced with minimal environmental and human rights impacts.
Iridium’s strategic relevance is rising rapidly, particularly due to its irreplaceable role in proton exchange membrane (PEM) water electrolysis for green hydrogen production. Its corrosion resistance and catalytic stability under extreme acidic conditions make it a critical enabler of global decarbonisation targets. In parallel, iridium’s use in satellite components, radiation shielding, precision coatings, and advanced medical isotopes further underscores its dual-use importance. Despite this, iridium has not yet been formally recognised on most national critical minerals lists, although its supply risk profile and industrial indispensability strongly support its inclusion.
As global demand accelerates and primary production remains constrained, efforts to stabilise and secure iridium supply will depend on coordinated action across industry and government. Investment in recycling infrastructure, advanced refining technologies, and strategic reserves will be essential to offset production inelasticity. R&D into load-reduction strategies and iridium-alloy innovations may provide medium-term relief, but they cannot fully eliminate the material’s criticality in hydrogen systems and aerospace applications.
Iridium’s future supply landscape will be shaped by a convergence of industrial demand growth, geopolitical uncertainty, and sustainability expectations. With few viable substitutes, low production elasticity, and concentrated geopolitical exposure, iridium represents one of the most strategically sensitive elements in the clean energy transition. Building a resilient, transparent, and diversified iridium supply chain will be fundamental to supporting global decarbonisation, medical resilience, and space exploration ambitions.
Current primary iridium producers
Iridium substitution
In proton exchange membrane (PEM) water electrolysis, iridium is the preferred catalyst on the oxygen evolution reaction (OER) side, owing to its unmatched stability in acidic, high-voltage environments. While platinum, ruthenium, and various metal oxides have been trialled as substitutes, none offer comparable corrosion resistance and catalytic lifetime under commercial PEM conditions. Ruthenium shows higher catalytic activity but suffers from rapid dissolution unless stabilised through alloying, while transition metal oxides and perovskites degrade in acidic environments or require higher overpotentials. Current substitution efforts therefore focus on reducing iridium loadings through dispersion engineering, thin-film coatings, and core-shell structures, rather than complete replacement.
In PEM fuel cells, iridium plays a smaller but critical role, often alloyed with platinum at the hydrogen electrode to enhance catalyst stability during frequent start-stop cycles. Substituting iridium in this role is being explored using durable carbon supports, nickel-based systems, and advanced nanostructured platinum alloys. However, under the acidic conditions and dynamic load cycling of PEM fuel cells, iridium remains essential for performance retention. In alkaline fuel cells, which are more tolerant of non-precious metals, iridium substitution is more feasible, although these systems are not yet mature for large-scale deployment.
In the chemical sector, iridium serves as a high-efficiency catalyst in reactions such as the Cativa process for acetic acid production, where it has largely displaced rhodium due to cost-effectiveness and performance. While other transition metals can catalyse similar reactions under modified conditions, iridium offers unmatched selectivity and stability, particularly in continuous flow systems. Efforts to substitute iridium in hydrogenation, hydrosilylation, and carbon–carbon bond formation typically involve base metals like iron or cobalt, but these often require harsher reaction conditions or produce more side products. As such, iridium remains the catalyst of choice in many fine chemical and pharmaceutical synthesis routes where high turnover numbers and long catalyst life are critical.
In electronics, iridium is used in hard disk drive platters, memory devices, and as a barrier layer in semiconductor fabrication due to its oxidation resistance and thermal stability. Substitution with tungsten, titanium nitride, or ruthenium is being evaluated for next-generation semiconductor nodes. However, iridium’s ability to form stable, conductive, and ultra-thin films makes it difficult to replace in nanoscale device architectures, especially where process compatibility and electromigration resistance are essential. In spintronic and quantum materials research, iridium’s strong spin–orbit coupling is actively exploited, and potential substitutes remain limited or experimental.
In aerospace and high-temperature applications, iridium is used in thermocouples, crucibles, spark plugs, and satellite thrusters, often alloyed with platinum or osmium. These components operate under extreme heat, oxidising environments, and mechanical stress. Alternatives such as hafnium, tantalum, tungsten, and ceramics may offer partial substitution in specific cases, but they generally lack iridium’s combination of thermal resilience, oxidation resistance, and long-term mechanical integrity. Substituting iridium typically requires a full redesign of system architecture or a trade-off in lifetime and reliability, particularly in deep-space or defence-grade systems.
In medical applications, iridium is used as a radioisotope (Ir-192) in brachytherapy for cancer treatment. Substitution options include isotopes such as cobalt-60 or cesium-131, but these differ in gamma emission profiles, shielding requirements, and dosage precision. Iridium’s properties make it particularly effective for high-dose-rate treatment of prostate, cervical, and breast cancers. Outside of radiotherapy, iridium is used in biomedical electrodes and sensors, especially in neural stimulation, due to its biocompatibility and electrochemical stability. While platinum or titanium can substitute in some roles, they may suffer from signal degradation or biofouling over extended use. In advanced applications such as brain–computer interfaces, iridium remains indispensable for signal fidelity and implant longevity.
In glass and optical manufacturing, iridium is used in crucibles for growing high-purity synthetic crystals such as laser-grade YAG and sapphire. Alternatives include platinum-based alloys, rhenium, or coated ceramics, but these materials generally exhibit higher contamination rates or lower lifespan under high-temperature oxide exposure. Iridium’s ability to retain dimensional integrity at temperatures above 2,000°C makes it the preferred material for producing optical-grade components where purity and mechanical stability are paramount.
In decorative and alloy applications, iridium is used to harden platinum jewellery and improve scratch resistance. It can be substituted with ruthenium or osmium in some alloy systems, although these may alter the metal’s appearance or workability. For aesthetic coatings, rhodium is often used instead of iridium, particularly in white gold and silver finishes. Given its niche role in this sector, substitution decisions are typically guided by cost and market positioning rather than technical necessity.
In emerging technologies such as OLEDs, photoelectrocatalysis, and advanced sensing, iridium organometallic compounds are central to research. Substitutes such as platinum or copper complexes are under investigation, but matching iridium’s photophysical properties, particularly in phosphorescent emission and redox cycling, remains difficult. As device miniaturisation and power efficiency targets become more stringent, iridium’s role is expected to expand, making substitution a longer-term challenge for materials science.
Overall, iridium substitution is limited by its unique chemical, thermal, and electrochemical characteristics. In most industrial and strategic applications, complete replacement is not currently feasible without sacrificing performance, reliability, or system longevity. Instead, the focus is on reducing iridium intensity through catalyst design, alloy engineering, and recycling. As demand rises from green hydrogen, aerospace, and medical sectors, substitution will remain highly constrained, reinforcing the need for improved material efficiency, recovery technologies, and critical mineral policy alignment to secure iridium’s long-term availability.
Iridium price in context, 1995 to 2021
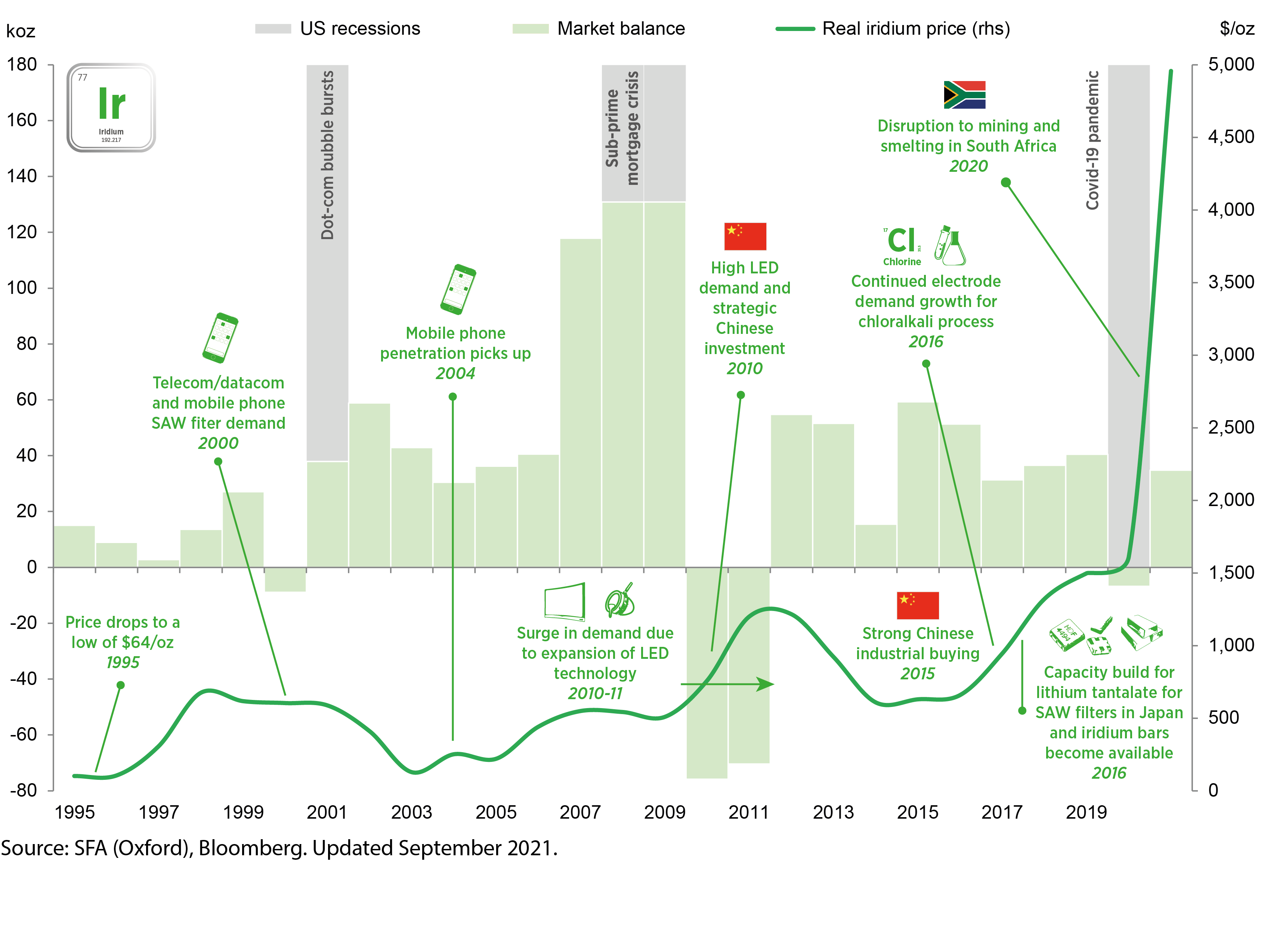
Iridium market balance
koz | 2016 | 2017 | 2018 | 2019 | 2020 | 2021 | 2022 | 2023 | |
Primary iridium supply | |||||||||
South Africa | |||||||||
Russia | |||||||||
Zimbabwe | |||||||||
Other | |||||||||
Total iridium supply | 275 | 275 | 275 | 285 | 235 | 315 | 270 | 270 | |
Iridium demand |
|||||||||
Jewellery | |||||||||
Hydrogen | |||||||||
Automotive | |||||||||
Chemical | |||||||||
Electrical | |||||||||
Other | |||||||||
Total iridium demand | 225 | 235 | 230 | 240 | 235 | 255 | 270 | 265 | |
Iridium market balance | |||||||||
Iridium balance | 50 | 40 | 45 | 45 | 0 | 60 | 0 | 5 | |
Iridium price history | |||||||||
Iridium price (USD/oz) | 575 | 896 | 1,283 | 1,480 | 1,629 | 5,075 | 4,464 | 4,682 | |
Iridium price (GBP/oz) | 429 | 694 | 967 | 1,160 | 1,268 | 3,862 | 3,620 | 3,765 | |
Iridium price (EUR/oz) | 521 | 792 | 1,092 | 1,322 | 1,425 | 4,288 | 4,245 | 4,330 | |
Iridium price (CNY/OZ) | 3,829 | 6,044 | 8,536 | 10,225 | 11,220 | 32,751 | 30,011 | 33,165 | |
Iridium price (ZAR/oz) | 8,413 | 11,934 | 17,195 | 21,379 | 26,757 | 74,685 | 72,872 | 86,414 | |
Iridium price (JPY/oz) | 62,480 | 100,445 | 141,993 | 161,354 | 173,688 | 557,847 | 586,379 | 658,508 | |
Source: SFA (Oxford)
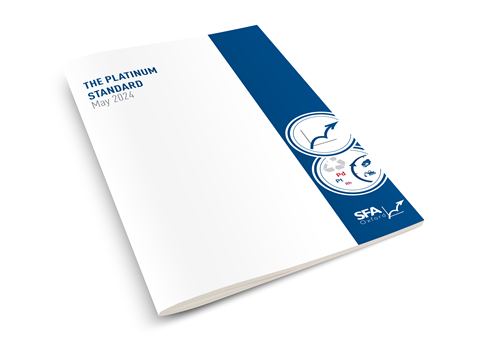

Linked iridium market reports
In response to requests for more regular iridium market intelligence, we now produce a bespoke quarterly iridium market report that allows you to keep up to date with this market.
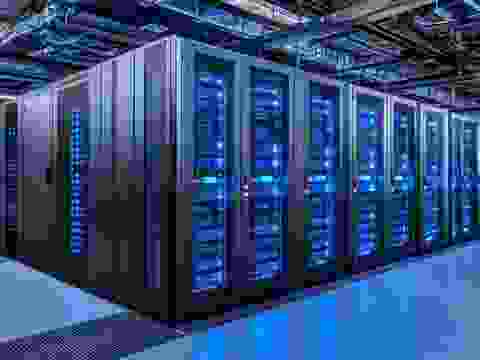
Meet the Iridium team
Trusted advice from a dedicated team of experts.
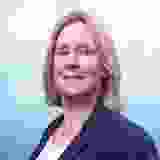
Dr Jenny Watts
Head of Clean Energy & Sustainability
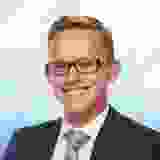
Alex Biddle
Senior Mining Analyst
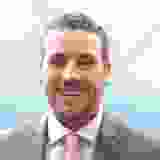
Jamie Underwood
Principal Consultant
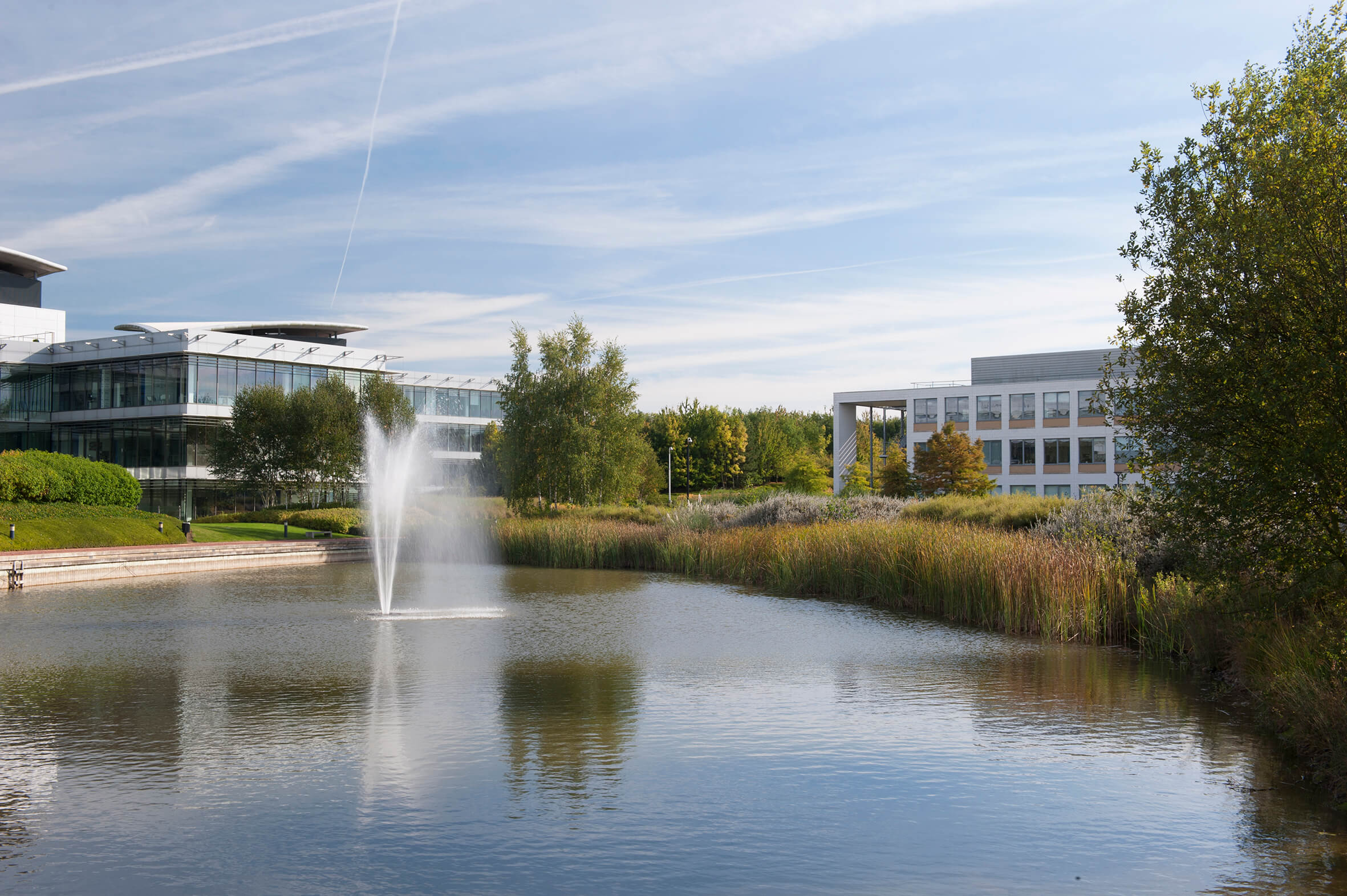
How can we help you?
SFA (Oxford) provides bespoke, independent intelligence on the strategic metal markets, specifically tailored to your needs. To find out more about what we can offer you, please contact us.